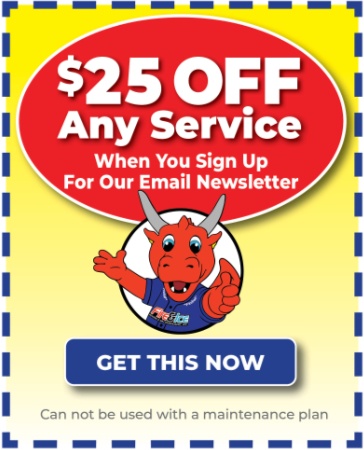
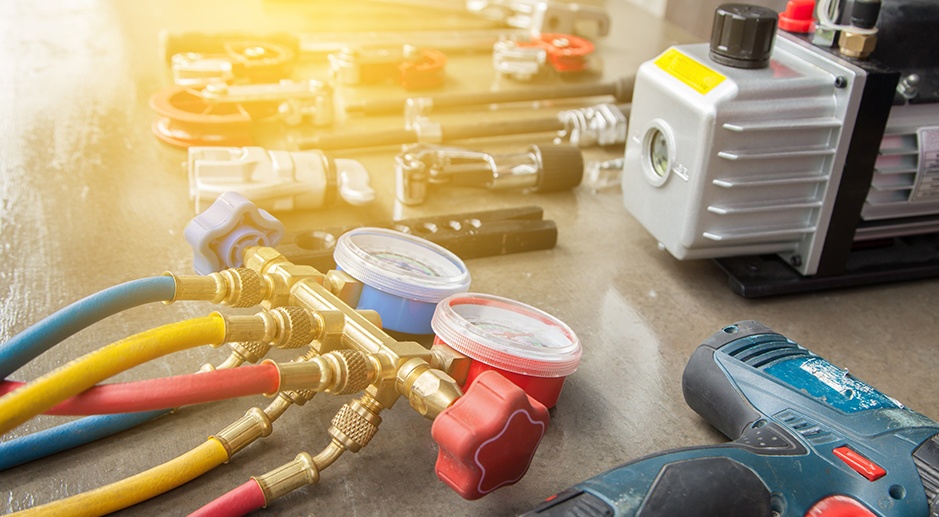
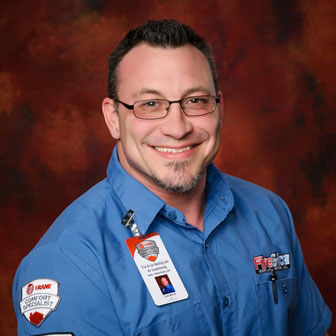
Author:
Revised:
November 11th, 2020
Do you know what it means to commission newly installed heating and cooling equipment?
If you don’t, you’re not alone. In fact, there’s a decent chance your equipment wasn’t commissioned when it was installed.
This is a problem. It’s a problem we here at Fire & Ice have been seeing for years. The problems aren’t always obvious, and they’re not always immediate. But it’s those facts that make it easier for companies to cut corners during the installation process.
They still get your money, but in the long-run, you’re paying more in numerous ways.
This is a subject I’m very passionate about because it gets to the heart of how we do business here at Fire & Ice. Commissioning isn’t always quick, or easy, and it’s rarely the cheapest option (upfront, at least). But it’s the right thing to do for the customer.
Want to figure out what commissioning is, and why it matters? I hope you do, and I hope you’ll read on.
What Is HVAC Commissioning?
Commissioning is a complete startup process for new heating or cooling equipment, to make sure it’s operating within manufacturer specifications and the parameters of your home. Full commissioning takes about 45 minutes per major equipment type or 60-90 minutes for a full system.
The elevator pitch for homeowners goes something like this: the benefit is knowing that your system is operating properly on all levels and at all times. Operating at these correct levels increases the efficiency, comfort, and longevity of your system. Commissioning also provides baseline metrics for your system in case it starts having trouble and needs maintenance or repairs.
We’re going to dig into each of those aspects below, but in a nutshell, it all relates back to these benefits.
HVAC vs. IKEA
Ever put together an IKEA shelf or other piece of furniture? There may have been some complexity, but for the most part, you followed the instructions, put each part where it belonged, and had a functioning piece of furniture in an hour or so.
HVAC isn’t like that at all.
The big misconception is that HVAC equipment comes out of the box ready to go, like a refrigerator. Or that each system is like an IKEA shelf, requiring some assembly but more-or-less the same from job to job.
You might have the same brand or model as your neighbor, but the intricacies of your home and HVAC system make each installation unique. It also means more can go wrong between jobs unless you know what to look for.
What are some of those unique properties?
- Dimensions of your home
- Placement, size, number, and efficiency of the windows
- How recently you insulated the home
- The distance of various rooms from the blower fan in your HVAC system
- Size and shape of the ductwork running through your system
- Fuel source (gas, propane, electric, etc.) and levels of gas or electric consumption
The end result is that each installation should be thought of as designing a system that matches your home. Some companies will have “one size fits all” solutions, which is where the misconception comes from. They don’t actually fit all, but they might tell you they do.
That’s also why commissioning is important. Because that “one size” on 10 different homes will be fine for some, mediocre for others, and horrible for some. If you’re unlucky enough to have one of these bad designs, you’re throwing away thousands in energy bills and years off of the life of your equipment.
A Comparison to Car Diagnostics
So you go in for a car appointment, and regardless of whether or not you have a specific issue, at least now and then you’re going to want to get a diagnostic.
These diagnostics can uncover underlying issues with your car that might otherwise fester into a larger problem in the future. And sure, it might not feel great to pay extra for a minor repair or replacement part, but you’re potentially saving yourself thousands of dollars down the line.
Commissioning reports are kind of like that.
So when a repair or maintenance technician comes to your home, if they’re only looking at the thing you think is causing a problem, they’re not doing their job well. As necessary, commissioning should be run again by a service technician to see what the underlying problems with a system might be. If any of the levels are off from when the unit was installed, they have a starting point for inspection.
What Occurs in AC, Furnace, and Heat Pump Commissioning?
We’ve talked a lot about the benefits of commissioning reports, but not what exactly goes into them. Let’s fix that now.
At Fire & Ice, we do a 57-point commissioning of equipment. We’re not going to list all 57, and some of them are dependent on equipment type, so not every report will have each one. But we’ve listed several of them below, to give you a sense of what readings we’re taking during a commissioning report.
- Temperature drop rates at various stages of cooling
- Temperature rises for various stages of heating
- Static pressure readings at each stage
- Amperage of the blower motor
- Gas pressure at each phase of the heating or cooling process
- CFM (cubic feet per minute) of airflow throughout the ductwork
- Refrigerant pressures at each phase of the cooling cycle
Here’s an example of a commissioning checklist from EnergyStar. It’s a good example of the highly technical information that should be collected to ensure a quality installation. Some manufacturers even require that their checklist be completed before they’ll honor warranties.
The list above could be longer, but hopefully, that gets the point across. Each of these, if improperly calibrated, could represent a significant problem.
Case Study: Blower Motor Tuning
Your blower motor is the major piece of equipment that is going to be used in both heating and cooling cycles. It is what moves the air throughout your system.
Depending on the size of your home and other factors, each unit will have a capacity or size, which relates to its power. Power is represented in tonnage. So you might need a 3-ton system for your home.
The blower motor, however, comes with factory settings that don’t account for variances in home size and equipment. Out of the box, it’s not properly calibrated to a specific unit capacity.
If an installer simply installs the blower motor and doesn’t test or calibrate it, you have a reasonable chance of its power settings being incorrect for your system. For example, its factory setting might be calibrated to move air in a 4-ton system when you only need a 3-ton.
Mechanically, this means that air will move too fast across the evaporator coil, which will waste energy and make your home less comfortable. It can also create pressure issues in your ductwork, which should similarly be sized for a 3-ton unit. Worst case scenario, you have airflow backups in sections of your ductwork, which causes the system to work even harder. This will also cause leaks in the ductwork over time, creating additional inefficiencies.
RELATED: HVAC Ductwork: Best Practices for Cleaning, Modifying and Care
Long-term, your system will cost you thousands more, and will likely die years before it would otherwise.
This isn’t a hypothetical situation. We’ve seen this too often. All of that, simply because the HVAC installer didn’t know or care enough to check the pressure and airflow levels, and adjust the system accordingly.
Digital vs. Analog Commissioning Gauges
At Fire & Ice, we use digital gauges as opposed to traditional analog gauges. The image immediately above this section shows both an analog (left) and digital (right) gauge, for example.
However, digital gauges offer more information, more accuracy, and a better overall image of a system’s performance.
It’s like an analog vs. digital speedometer in your car, but multiplied dozens of times. For example, instead of having to “eyeball” gas pressure at various heating stages, and take multiple readings just to get a proper view of system functions, the digital gauges can give us more information, more accurate information, and deliver all of those things faster.
It’s a more complete, accurate picture of your system’s health.
Why Do These Levels Matter?
The blower motor example above is a great one to show what can happen if a system isn’t commissioned thoroughly.
The part that most don’t realize, though, is that those blower motor problems might not manifest for 8-10 years. Granted, your energy bills will be higher the entire time, but the difference between “ok” heating and cooling and “great” is often something an average homeowner doesn’t know how to measure.
This is what allows some companies to get away with skipping these steps.
There are at least a couple other important reasons to have a thorough commissioning report:
- Static pressure. This is the #1 culprit we see, either to improperly calibrated equipment, improperly sized ductwork, or both. If your old system died before it was 15-20 years old, chances are it was due to complications from static pressure. Even if the final straw was something else, it often relates back to these pressures creating stress across the entire system.
- Maintenance Visits. Whenever we have an issue with a system that we’ve installed, one of the first things we do is reference the commissioning report and check any relevant items again to see how the system is performing. It’s like getting a physical at a doctor’s office. Your healthy levels are a baseline, and if you start feeling pain, your doctor will check those vitals again to see what has changed.
Proactive Measurements to Ensure Proper Installation
Ideally, your system is installed correctly the first time. We’ve had calls, though, where we’re cleaning up someone else’s mess.
The answer to this is thorough measurements at the time of the estimate and installation. Our technicians perform a Manual J Load Calculation of your home, and often a Manual D Load Calculation of your ductwork. By knowing the parameters of each, a properly installed system should have good initial “vitals,” to use the doctor analogy from above.
Why Doesn’t Everyone Do Commissioning?
Commissioning is rare. But why is that? The answer, unfortunately, is simple.
Cost.
Let’s talk about what goes into setting up a proper system of commissioning across a company:
- Time. If you’re commissioning to ensure proper function, you’re not running off to the next job to get paid more for the day.
- Tools. It requires a digital manifold, digital manometer, an amp meter, voltage meter, thermometers, and more. An entire kit is required to perform these checks.
- Training. HVAC installers aren’t always trained on these tools by default. Additional training is often needed to ensure proper procedures are adhered to.
- Labor. I was hoping I could have “Four T’s” here for the alliterative effect, but oh well. In any case, labor costs won’t skyrocket for you with commissioning, but it is an extra upfront cost. We firmly believe it’s in your best interests in the long-run, but it often means the company that’s doing commissioning isn’t coming in with the lowest estimate. You get what you pay for.
So if the customer is unaware that these steps should be taken with each installation, how many companies do you think just ignore it? We don’t have an exact answer to that question, but from decades of personal experience in the industry, I can say that the answer is “too many.”
Want to make sure you’re getting this service with your installation? I have two things you can do right now:
- Download our HVAC Contractor Checklist (linked below). It will give you the ammunition you need to ask the right questions of whoever you hire for your next job.
- Ask your contractor what measurements they take during commissioning. And if they don’t do this or stumble through a short response that doesn’t include many of the factors listed above, don’t be surprised.
- Give us a call or schedule an estimate by clicking the button below. We’ll be happy to walk you through the full process, to ensure your home is getting the attention it deserves.
If you’re in Central Ohio, we’re looking forward to speaking with you. And regardless, we hope this information was able to make your day just a little bit better.