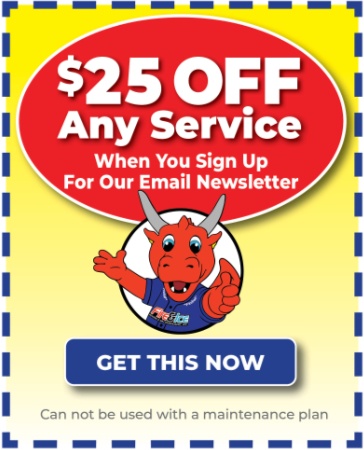

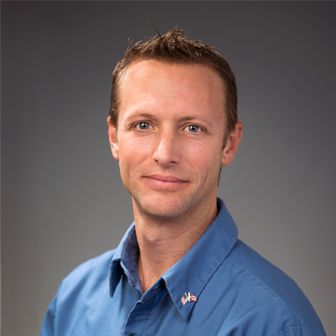
Author:
Revised:
November 2nd, 2021
Research indicates that 70-90% of AC/heat pump/furnace systems in homes are incorrectly installed and are susceptible to performance issues.
Let that number sink in.
If you’re thinking about spending thousands of dollars on a new system, and you’re unsure about how to spend that money wisely, this article is for you. The most important day in the life of any HVAC unit is the day of installation. A sloppy job results in more repairs, and possibly a shorter lifespan for the equipment.
At Fire & Ice, we have been asked thousands of questions regarding the installation process over the years. We’ve compiled a few answers that we hope will clear up some confusion.
What happens during the installation process? And how is Fire & Ice’s installation different from anyone else’s in Columbus, Ohio, and the surrounding Central Ohio area?
There are two things that should be on every HVAC contractor’s mind during the day: What’s in the best interest of the customer? Are they satisfied throughout the whole day? And second, is the machine working the way we said it was going to?
How Long Will the Installation Take?
Installation of a full system is a full-day process. The day starts between 8:00 and 9:00 a.m. and can last until 6:00 p.m. -- sometimes longer. The removal of the current system can take 1 to 3 hours, and the installation of new equipment can range between 4 and 7 hours.
Any modifications to the existing ductwork, gas lines, and electrical wiring can take longer for the system to be installed.
If there’s a lot of ductwork involved, it might turn into a two-day job.
Before Installation Day
With the installation of any indoor or outdoor unit, we pull the required permits, and not everyone does.
These are some of the common reasons your contractor may not pull permits:
- They aren’t licensed. Unlicensed contractors can’t pull permits.
- Pulling permits costs time and money. Just as some contractors don’t perform Manual J Load Calculations, some don’t pull permits.
- They’re afraid of the inspection. Permits lead to inspections. Some contractors are afraid to face a third-party inspector’s scrutiny.
Installation Day
We will show you pictures of the installers who are coming showing up so when someone shows up at your house, you will recognize them. We do that so you’re not faced with total strangers.
On the day of installation, our professionally trained crew will call you on the way to your home to confirm the appointment. If we’re installing a full system, we send two people, one inside and one outside.
And they will arrive in an actual Fire & Ice truck, which is not common. I’ve had people tell me that they told the installers, “Go away,” because the company’s name on the truck wasn’t the same as the HVAC contractor they’ve contracted with.
Our installers wear the same uniform as our salespeople. They will be wearing a mask, with shoe covers to protect your floors. We will use drop cloths, and they will be clean. We clean those drop cloths daily, and we’re not talking about shaking them into the wind. We wash them back at our home office. We’re probably the only HVAC company in Columbus that has a washer and dryer.
We go over the job with you before we start. It seems like an easy thing to do, but most companies just show up and start working. The lead installer will take the time when they get there to review the job, tell the homeowner what’s about to happen, so there’s no miscommunication.
That’s what we do just to prep for a job. It’s a process, and it takes time, and it’s in the customer’s best interest.
Next, they will properly remove and dispose of any existing equipment. Next will be the installation of the new equipment.
We would always have a new outdoor pad for the AC/heat pump. The only time when we wouldn’t do it is if someone poured their own concrete pad. Usually, we put down gravel so the pad is level, because it does look nicer when it’s level. We also have practical reasons for making it level. There’s oil in that compressor. You don’t want oil only on one side, and refrigerant won’t flow as well in a tilted unit.
We have someone on standby in the office in case there’s a problem that the person in the field can’t resolve.
Disposing of Refrigerant
During the install, what we’ll be doing differently is following EPA regulations for disposing of refrigerant. We don’t cut corners.
Your existing air conditioner contains a refrigerant that needs to be removed before a new one can be installed. According to EPA standards, it is unlawful to openly vent this refrigerant into the atmosphere.
A device known as a recovery machine must be used, along with a recovery tank, to safely and legally remove the refrigerant in the existing central air conditioner system. This is the only process that allows for the safe removal and proper handling of the refrigerant.
There’s refrigerant in that old system, and there is an EPA regulation that you vacuum it down, to pull that R-22 out into a proper EPA tank. This is instead of something called bleeding or venting, which is where you poke a hole in the refrigerant line and let it leak out, which is against the law.
Brazing
After the line set is fitted to the service valves, they must be brazed in. Brazing, a form of welding, is a process using two gases (oxygen and acetylene) and a filler rod made of an alloy metal and silver to join the copper line set and service valves. The valves are heated to a minimum of 1200 degrees Fahrenheit, or until the filler rod will flow to weld the connection.
If this process is completed properly, the copper line set, the filler rod, and the service valve are all melted together for a tight, leak-free connection.
We braze with nitrogen, which sounds simple, but most companies don’t do it. Nitrogen-based brazing is used during installation to prevent contaminants from entering your HVAC system.
Possible Complications in the Installation Process
Occasionally an installation throws a curveball at us. The thermostat’s wiring can be an issue, and if the wires from the thermostat aren’t properly connected to the furnace, we have a problem.
The electrical panel could be bad. We’re not electricians. Plumbing issues can pop up. We ask if there’s ever a problem with drains. Sometimes we have to break through drywall for ductwork. That’s a complication.
Most of the unforeseen issues are client-based. Homeowners decide they want something moved, and they think it’s no big deal. It is a big deal in our world. Relocating HVAC equipment is complicated and can be pricey.
A complication might arise from a miscommunication from our side. We present a lot of different options when we’re sitting down with homeowners. Although we agreed on one, the client may have another idea of what we agreed on.
Commissioning Process
Our installers are required to commission (test) the HVAC equipment before they leave.
The startup and commissioning process is done after the system is completely installed and ready to operate. Commissioning can take anywhere from a half-hour to an hour and a half. We use digital gauges because they’re more accurate. Most install technicians don’t have them, because they’re 1099, they would have to pay for them themselves.
When we’re commissioning and we discover a problem, our techs don’t just write down the number and move on. We have to figure out why there’s a problem. Commissioning is the right thing to do. Other HVAC companies may claim to do this, but common practice suggests otherwise.
A good installer will check the thermostat operation, system sequence of operation, and multiple other areas. While the system is operating, the following data is important to collect to ensure proper operation within manufacturers' specifications:
- Suction and liquid line pressure
- Suction and liquid line temperature
- Superheat
- Subcooling
- Outdoor ambient dry bulb temperature
- Indoor ambient dry bulb temperature
- Indoor wet bulb temperature
- Return air temperature
- Supply air temperature
- Static pressure from return side, supply-side, and total static readings
- Temperature drop calculated
- High voltage current reading
- Amperage on the blower motor, outdoor fan motor, and compressor
- Low voltage current reading
- Line set length
- Amount of refrigerant, if any, added to the system
- Distance above or below the outdoor unit in relation to the indoor coil
- Blower speed tap/CFM recorded
This is the basic list of the proper data that should be known and recorded. This is the only way to know for sure how the system is operating and if it is within manufacturing specifications. If any of these do not fall within manufacturer specifications, your system may not be warrantied by the manufacturer.
Once the equipment is commissioned, the installers will review with you everything that was done during installation and go over any questions you may have. They will walk you through where the filter is and how to change it. If a new thermostat has been installed, they’ll show you how it works.
Final Quality Inspection (FQI)
A week or two after installation, a Fire & Ice representative will return to your home to ensure everything is running smoothly, to make sure you understand your thermostat and comfort options, and to inspect the quality of the installation. If anything is amiss, it is reported to our training and management staff and is used to inform changes to our installation practices and training.
We’re proud to be the only contractor in the area who will return for this visit to look you in the eye to make sure you’re satisfied with the job that was done.
We think that FQI is an essential part of the installation process.
We take pictures before, sometimes during, and after. That helps us to make sure we did it right. If there’s an error, we can look at the pictures and figure out before we get there what the problem might be. It also helps with warranty issues. We can show that we did things right if something goes wrong and we get accused of a poor installation.
Important Steps That Are Sometimes Skipped
The reason other companies don’t do some of the steps we’ve talked about is that it takes more time or it costs too much money. Doing things right takes longer. Doing things right costs money.
To most installers, time is everything. They don’t care about the client. If there’s a process they can cut, that means they can get out of there quicker, they get paid quicker. Maybe they can get done quickly enough to get another job. They get paid by the job, not by the hour.
Our HVAC contractors at Fire & Ice get paid by the hour. They also get a bonus for installations that are trouble-free. That allows them the time to do things right. Because if it’s not done right, it’s not worth doing.
Your Next Steps
I hope by now you have a better understanding of what typically goes into installing a new heating and cooling system.
One final thought:
The brand of equipment matters less than the quality of the installation. It is true that a lesser quality piece of machinery will not last as long as a better one, if the installation, maintenance, and usage are the same.
It’s like a Yugo versus a Cadillac. The Yugo, even if it’s properly maintained, will have more problems than the Cadillac, if it also is maintained. A better-quality brand of furnace will have more comfort options than an entry-level one, which is fixed-speed, single-stage, with a single-stage of heating or cooling. If you have comfort concerns - such as excessive dry air in the winter, or mugginess in the summer - a cheap furnace or air conditioner can’t address those.
Any dealer can install Trane or Carrier if they want to, as we do. But the installation will be the main difference in quality. For your peace of mind, take a look at our contractor’s checklist to see how companies measure up:
And if you’re interested in talking to Fire & Ice about your next Columbus, Ohio, HVAC project, we’re happy to listen. Enter your zip code in the graphic below to get started.
In the meantime, here’s a bit more about us that you can read:
How to Know Your Heating & Cooling Company Cares
Top 7 Things to Look for When Choosing an HVAC Company
10 Things to Get Out of an HVAC Sales Appointment